PELLETS
BRASIL
BRASIL BIOMASSA
A Brasil Biomassa é especializada no desenvolvimento das plantas industriais de produção de pellets. Na fase industrial iniciamos com a área de recepção de matéria-prima para o processo industrial. Para minimizar os custos a unidade industrial de processamento de pellets deva ser construída próxima da área de matéria-prima (transporte pneumático até a tremonha de matéria-prima).
A planta industrial de pellets deve operar ininterruptamente, requerendo um contínuo abastecimento de biomassa para a geração de energia térmica (resíduos descartados) e de matéria-prima (cavaco, wood chips, serragem ou micro-pó) para o processo industrial.
Sistema de moegas. Instalada no nível inicial do projeto industrial para poder receber a matéria-prima de forma manual ou automática, com a função de armazenar a matéria-prima para dosagem no sistema industrial de secagem . Sistema de transporte ou redlers que são transportadores horizontais com sistema de elos de correntes. Este transporte foi desenvolvido especialmente para atender as situações mais exigentes que não permitem resíduos, separação de produto e baixa produtividade.
Silo de abastecimento de matéria-prima. O silo se baseia em painéis pré fabricados que quando interligados por meio de parafusos (sem solda) se travam formando a estrutura de sustentação do conjunto.
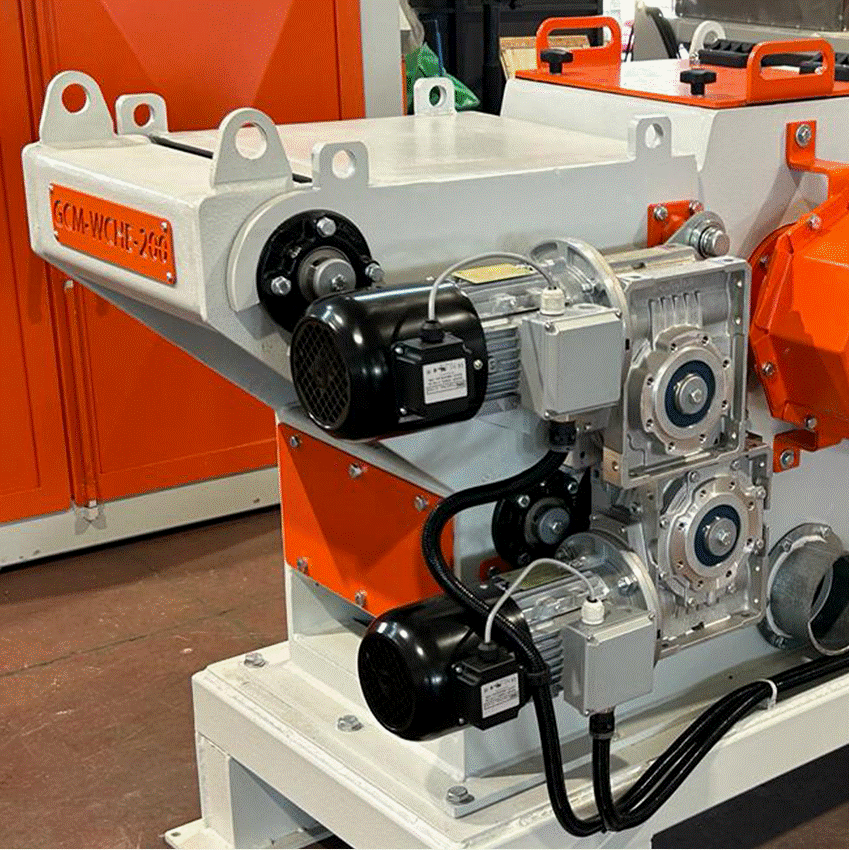
A matéria-prima seca será transportada para a fase de refinação e de moagem (refinação de modo que a partícula seja reduzida ao tamanho máximo 2mm – redimensionamento da matéria-prima) e trituração para ser homogeneizado relativamente à dimensão, através de moinhos de martelos.
Moinho de martelos. O material é introduzido verticalmente pela parte de cima da máquina. Martelos planos de aço, rodando em alta velocidade, quebram materiais alimentados até virarem grãos/pó (definido pela malha da peneira escolhida).
Elementos estacionários de refinamento no moinho ajudam na redução de tamanho.
Sistema de exaustão e ciclone. Utilizados nos sistemas de exaustão, seja no processo de moagem, peletização ou extrusão. Os ciclones são projetados para atuarem com alta eficiência na retenção e separação de partículas eventualmente aspiradas no processo de exaustão.
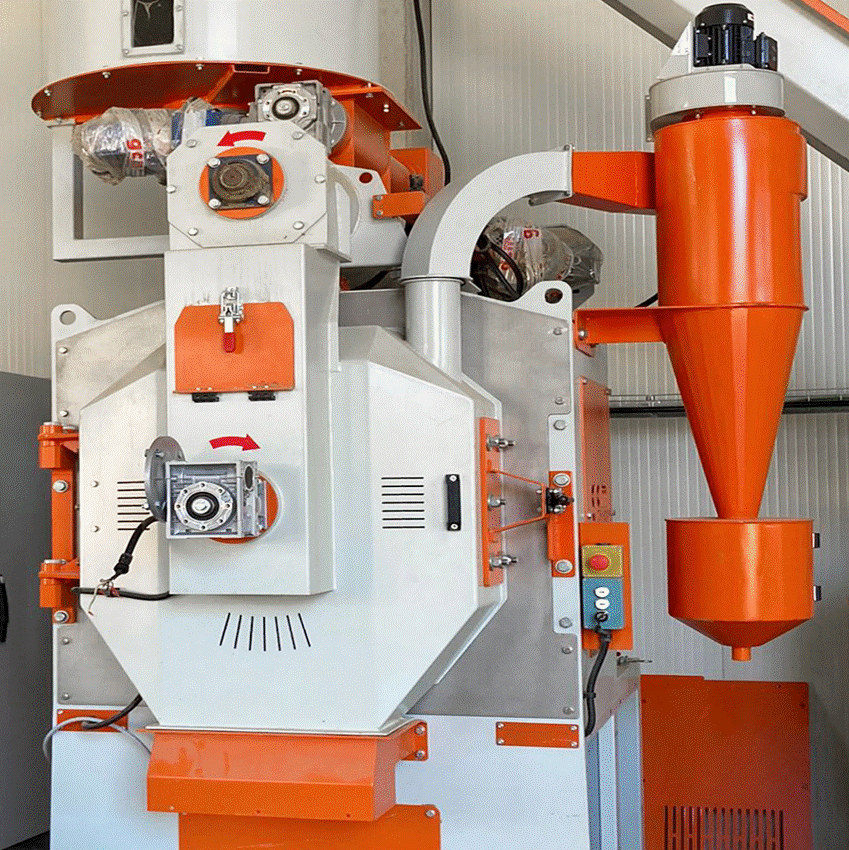
Nesta fase seguinte iniciamos como processo de geração de energia térmica e de secagem industrial da matéria-prima úmida que passou pelo processo de alimentação e preparação industrial. A matéria-prima (serragem, maravalha ou cavaco de madeira) são transportados para a secagem industrial (obtenção de um conteúdo de umidade no máximo 14%).
Tecnologia de geração de energia térmica é pelo sistema da fornalha de alta tecnologia que é construída com aço carbono com coletor de gases. A fornalha de queima pirolítica é fabricada em estrutura metálica com revestimento por tijolo refratário em alumina, acoplado na parte frontal por um alimentador que faz a injeção automática de combustível conforme a necessidade de calor e gases para o secador.
Secador industrial, ventilador centrífugo, ciclone e válvula rotativa. O secador industrial é uma equipamento que realiza a desidratação da matéria prima. Possui pistas pesadas e rodado revestimento de alta qualidade. Isolamento e revestimento térmico no tanque externo.
Nesta fase industrial iniciamos como processo de refinação e de moagem industrial.
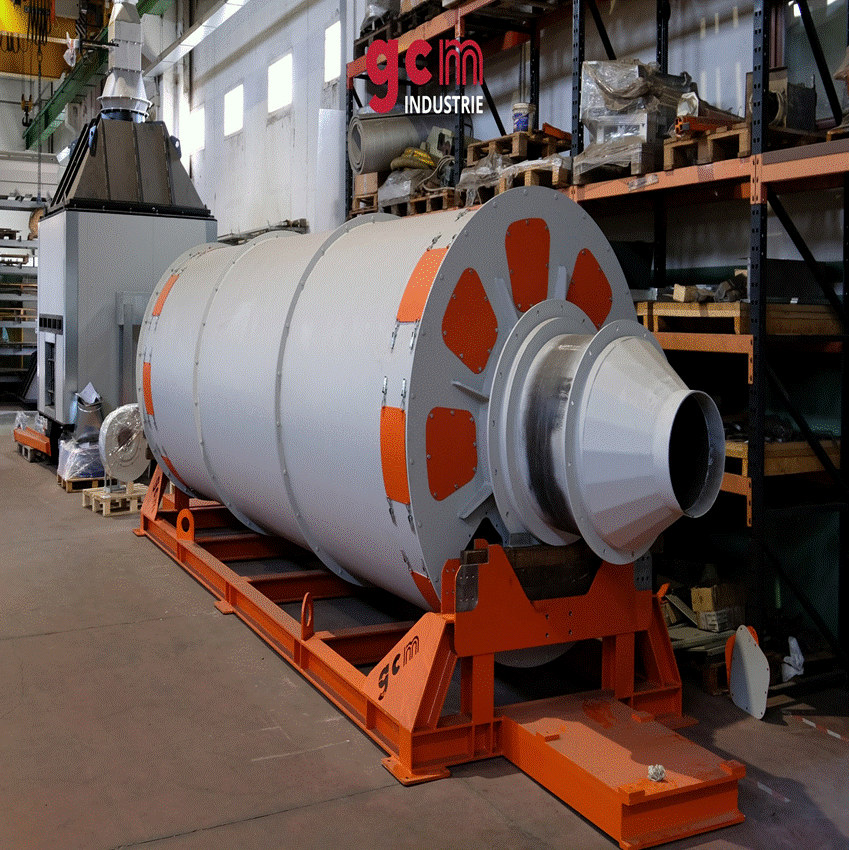
Após passar pela última refinação na unidade industrial, o material é prensado, com diâmetro de 6 ou 8 mm e comprimento entre 20 e 40 mm. No processo de prensagem é necessário um aquecimento até temperatura de 120-130 ºC (com recurso a vapor seco). Uma vez na peletizadora o material triturado é moído e acondicionado mediante o uso de vapor, que contribui para a umidificação superficial, atuando como lubrificante no processo de peletização. Assim, a adição de vapor contribui para que o aglutinante natural atue com maior facilidade sobre as fibras que compõem os pellets.
Após peletização, a temperatura dos pellets é normalmente cerca de 60 a 80 graus Celsius, e o teor de umidade é de cerca de 8 à 9%. Em seguida, a máquina de resfriamento utilizada para reduzir o teor de umidade para 6,5 %, de modo a garantir o armazenamento fácil. O sistema de resfriamento consiste numa câmara vertical, de onde os pellets caem em fluxo de contracorrentes, permitindo diminuir a sua temperatura. Esta corrente é gerada por ventiladores mecânicos que funcionam acionados por energia. Durante o resfriamento, os pellets tornam-se rígidos e perdem umidade podendo chegar a 6,5%. O consumo de energia nesta etapa situa-se próximo de 5 kW/ton.
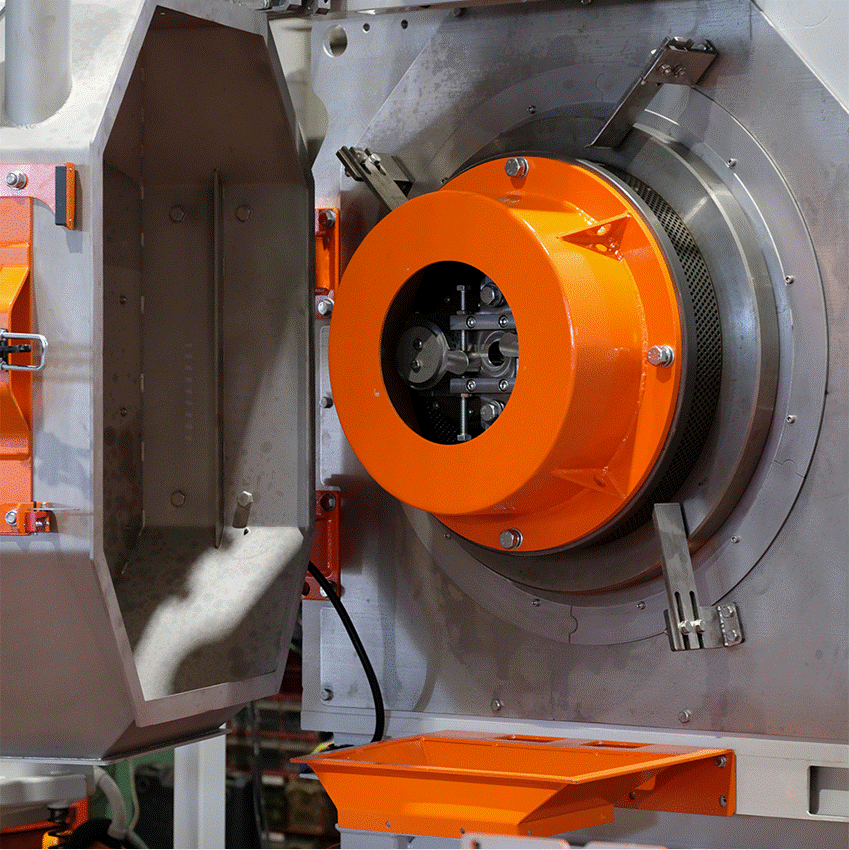
Sistema de embalagem industrial e ensacadora vertical com bobina plana. Estrutura porta recipiente de pesagem em chapa prensada e dobrada soldadas conjuntamente e portas e inspeção removível.
Recipiente de pesagem, feito de chapa de metal prensado e dobrado à carbono pintado, com cantos arredondados para evitar acumulações, completo com dupla porta de fundo, abertura pneumática para a descarga da pesagem.
Paletizadora automática. É projetado para movimentação dos sacos com produção média, para trabalhar em forma eficaz em espaços estreitos e para permitir o transporte de um único bloco. Isso é possível porque toda a máquina é constituída por uma estrutura única, que compreende também o painel elétrico e porque os pilares de suporte da mesma são telescópicos.
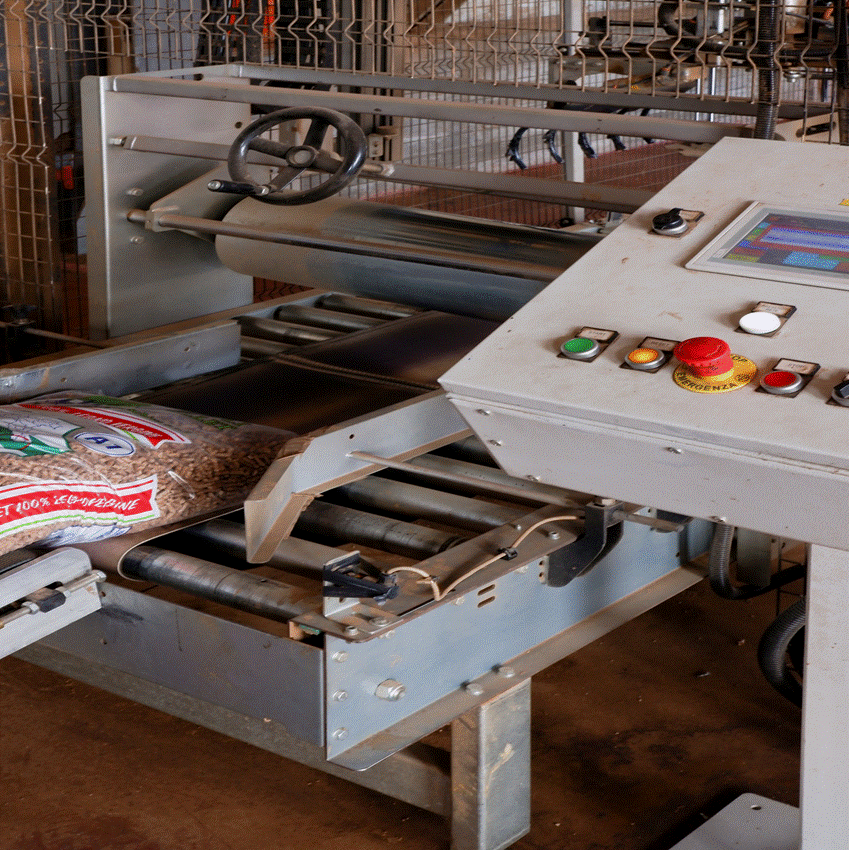